PRODUCTION

Preliminary Cost and Prescription
Thanks to the parametric structure, you can structure according to different preliminary cost needs. You can flexibly define your raw material, labor and general expenses, and make costs with seasonal agreed rates as well as daily rates. You can make any number of price calculations with flexible price calculation options.
You can define more than one production tree structure that suits the production structure of the company. You can define all the fields you need regarding technical sheets on stock cards and recipe screens. You can determine different production routes according to different product groups and automatically get your technical sheets from the system. You can design technical sheets and all production instructions as desired. You can use recipe information for all your form designs such as measurement tables, sewing and other production instructions, loading and packaging instructions, and requirement lists.

Production Planning
You can make production plans based on department and station, plan subcontracting prices and payment terms. You can follow plans based on work orders and departments, and make production plans based on color and quantity of work orders at different times.
You can track capacity according to production times and calculate station efficiencies. You can define section and station capacities according to the daily work schedule, and prepare band occupancy and capacity usage reports.
You can take control of production plans and prevent delays by tracking planned and actual production quantities and times. You can report flexibly on a production section and station basis.

MRP Raw Material and Demand Management
By running MRP (create demand according to production needs) according to production plans, you can ensure that the right raw material is in the right place at the right time. You can create purchase requests from production needs, and create requests according to order lead times by finding the system minimum stock amount according to free stock and goods in transit.
By defining minimum stock quantities, you can determine stock supply times and ensure that orders are created on time. You can determine supply times and warehouse stock level quantities in stock cards. You can define minimum order quantities and order multiples in the supply of your stocks and create your purchases accordingly.
You can create purchase orders based on demand from automatically generated purchase requests. You can create purchase orders from purchase requests generated as a result of MRP. You can get rid of idle stock costs with automatically generated raw material purchase requests based on production plans and free stock quantity.

Barcode Production Tracking
You can establish a scalable structure with different barcode tracking methods such as bundle, lot, semi-finished product and work order barcodes. You can use different barcode structures such as bundle and semi-finished product barcodes together and integrated. You can create a production control system in line with the needs of your departments by using different barcode types on a section basis.
With barcode systems such as companion barcodes and semi-finished product barcodes, you can perform online data collection operations quickly and without errors.
You can work with the web interface independently of the platform and make online integrations with the subcontractor workshops. With the web interface, you can work platform-independently via handheld terminal or PC. You can make online and controlled data entry and include subcontractor workshops into the system.

Product Quality Management
With web-based quality control (inspection) applications, you can perform online transactions and instantly take control photos and upload them to the control report. You can perform inspections by opening online control appointments via the web. You can control quality control processes according to AQL standards and create control lists based on product groups. You can instantly take photos during your control processes and upload them to the system.
You can report quality control appointments and results in the desired format. You can prepare graphic reports from control results.
You can track the product quantities to be controlled, minor and major error definitions according to AQL 2.5 standard systems. You can prepare different control lists based on product groups.

Work Order and Process Planning
You can create different process flows according to production processes and create different process plans according to different manufacturing types. You can create automatic process calendars according to parameters such as product group, difficulty level and order quantity. You can determine operations and workflow in sub-operations for each process.
You can provide control and authorization on a user and process basis, and analyze all transactions in the process follow-up by following the history with reasoned process revisions. You can determine the processes that users are authorized for, and establish an approval system with authorized users in process revisions. You can provide detailed authorization on a transaction basis.
You can design process reports as desired, prepare process delays and warnings as automatic e-mails. You can visually follow up completed and ongoing work, and prepare automatic e-mails for upcoming and delayed work. You can also perform process analysis in the desired format.

Purchasing and Raw Material Management
You can manage purchases according to work order needs, define color-size tracking for products with a single recipe, and perform free stock and needs analysis without creating a work order. You can define all product color sizes, components, and technical details in a single recipe. You can perform needs determination and purchase on a work order basis by department and station.
You can track raw material warehouse tracking as warehouse, shelf and work order reserve stock and free stock. You can manage the warehouse on a shelf basis and easily manage transactions such as purchasing, reservation, transfer to production. You can track all raw material and auxiliary material status in a single report. You can get rid of idle stock costs by seeing the needs, orders placed, reservations and stocks that need to be put into production, and by obtaining the raw materials required for production just in time.
You can track raw materials on a roll and batch basis for fabrics and accessories. You can track fabric stocks on a batch, lot and boiler basis. You can track warehouses instantly with barcodes using mobile handheld terminals and track quality control and tensile tests on a roll basis.
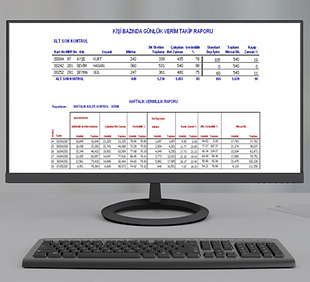
Operational Efficiency
You can perform productivity analysis based on personnel, line, department and factory. You can calculate effective and standard productivity based on study times. You can calculate productivity based on lost times and real working hours.
You can follow the study and actual efficiency calculations at the desired level. You can define standard and non-standard operations. You can make different duration analyses based on the sub-phases of the operations.
By working integrated with Pdks systems, you can automatically calculate the man-hour work performed by personnel entries and exits. You can calculate working hours by obtaining data from the personnel attendance tracking system. You can define different shifts and shifts for the business.