Univera
Warehouse and Shipping Management

StokBar Warehouse and Shipment Management
Stokbar Warehouse and Shipping Management is a software solution that helps businesses optimize their warehouse and shipping processes. This software supports a range of critical processes from warehouse design to inventory control, order preparation to shipment tracking.
Warehouse and shipping management is a business process that allows businesses to store their products in an orderly manner, perform stock control, prepare orders and manage shipping processes effectively. Regardless of the size of the business, effective management of these processes provides cost savings, customer satisfaction and competitive advantage.
Large warehouses, thousands of product types, complex shelves, pallets and shipping operations... Controlling these processes with manual management can lead to errors and financial losses. However, StokBar offers a flexible web-based solution that will help you manage your warehouse and production processes digitally.
StokBar Warehouse and Shipment Management
What are the benefits?
Warehouse and production operations are among the processes with the highest risk of error. Thanks to StokBar, you can digitalize these operations in the smallest detail and achieve perfection in your processes.
Minimizing human-based errors
Regular warehouses
Planned production process
Processes according to special classifications such as expiration date/shelf life
Defining rules specific to customers, channels and business partners
Product traceability
Performance traceability
System where all data can be tracked
Warehouse Management
Stokbar Warehouse and Shipment Management simplifies warehouse management. It increases intra-warehouse mobility by optimizing warehouse design. It also offers advanced tools for stock tracking and inventory management. This helps businesses reduce stock costs.
Shipment Management
Stokbar, which speeds up order preparation and packaging processes, simplifies shipping processes by integrating different shipping options. It offers advanced tracking and monitoring features to ship your orders correctly.
Minimize Manual Errors
Warehouse and production operations are among the processes where human errors occur the most. StokBar, by digitizing operations down to the smallest detail, you can minimize the possibility of errors in your business processes. In this way, you can reduce the risk of encountering incorrect product shipments, stock shortages and other errors.
Efficiency and Cost Savings
This software helps businesses increase efficiency in warehouse and shipping management. When combined with cost reduction strategies, businesses become more competitive. It helps minimize environmental impacts and contributes to carbon footprint reduction goals.
What are its functions?
StokBar was designed as a software that offers solutions for every stage of the warehouse and production processes. StokBar, which has various functions according to the personnel undertaking different tasks and the departments used, offers a series of smart functions to increase the efficiency of the business.
Intelligent warehouse management
Automation of displacement
Location tracking
FIFO/LIFO control
supply chain management
Inventory management
Traceability
Global SKU (stock keeping unit) management
All warehouse transactions are made via handheld terminal
Order preparation
Shipping, addressing
Palletizing
Quality processes
Labeling
RF-ID and voice control system
Detailed Features
StokBar, which stands out from its counterparts thanks to its detailed features, is a solution designed with the smallest details in mind for warehouse and production operations. StokBar offers you more than you want with these features.
Flexible definition
Creating a custom rule
Finished/semi-finished/raw material tracking
Backward traceability (lot, batch, party, serial number etc.)
Damaged/spoiled product control (classifications such as blockage, reserve, quarantine)
Product tracking according to special conditions such as FIFO, LIFO, FEFO
Loading optimization
Modules
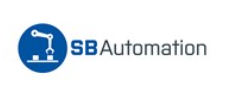
SBAutomation is our module that can be shaped with developments according to your needs, allowing you to collect information from various areas of production with OT/VT techniques. With SBAutomation, you can collect information from machines such as production lines, labeling machines, weighbridges, precision scales. With the collected data, you can create work orders and give commands to external systems and devices (printer, line, robot, forklift, etc.).

Just like in the inputs and outputs, you can provide controlled raw material feeding to production lines depending on production orders or production plans during production. With product recipe support, you can prevent incorrect material feeding to production thanks to SBManufacturing. You can have detailed data about the material used in production, and you can keep the times spent at the stations under control and make reports. When there is a change in production order, you can quickly implement the requirements. With SBManufacturing, your continuous or discrete production structures are supported. Your integrations with commercial packages can be provided instantly.

With SBMRP, you can calculate the resources/raw materials/semi-finished products required for your production accurately with all other input information such as sales forecasts, production plans, production recipes, production resources. You can save time by creating your orders automatically.
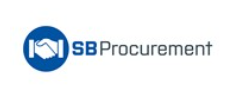
SBProcurement is the system where all necessary service and product purchasing processes for your business can be managed and reported. With SBProcurement, you can perform contract tracking, request creation, approval mechanism, user and supplier information, goods acceptance and reporting in various criteria.
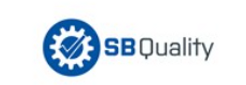
With the quality management module, you can define different quality value entry screens for different units in your business. SBQuality can automatically decide whether products are usable or unusable on a pallet, product, or batch basis, in accordance with the criteria you specify. You can create and print forms that you want to store outside of the digital environment by the system. You can automatically perform your shipment planning and product/pallet reservation processes in accordance with the criteria you specify with the SBQuality module.
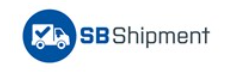
With SBShipment, shipments are organized with volume, weight and quantity-based results with the help of expandable parameters such as vehicle types and routes, and it allows you to visually carry out your loading operations faster and more efficiently. After loading on a vehicle basis, shipping points are automatically drawn and shown on the map according to the given priorities. You can use SBShipment as a manual vehicle filling method or automatically according to the priorities determined for the business, depending on your wishes.